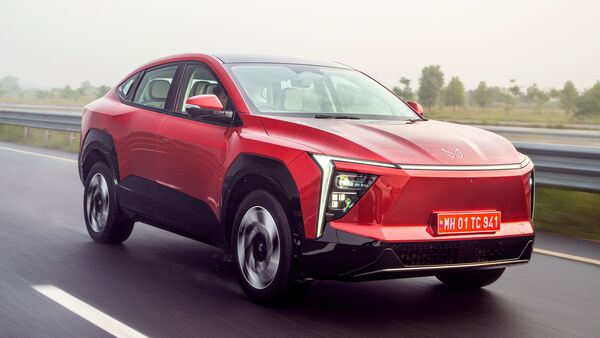
A closer look at Mahindra’s in-house developed battery packs
5 months ago | 5 Views
Mahindra has finally unveiled its much-awaited pair of battery electric EVs based on the brand’s in-house, born-electric INGLO platform. The two EVs in question – the BE.6e and the larger, more utilitarian XEV.9e – both are based on the same modular architecture which can accommodate SUVs of various sizes.
While Mahindra has sourced its battery cells from BYD, utilising the brand’s cutting-edge Blade battery technology (also found in the MG Windsor) the battery packs are developed and assembled under at the brand’s state-of-the-art facility for testing batteries at the Mahindra Research Valley in Chennai, under the watchful eye of the brand’s Chief of Global PRoduct Development, Auto Sector, R Velusamy.
Watch: Mahindra XEV 9e review: New benchmark for EVs in India? | Range and road test | First impressions
The battery packs, which feature LFP chemistry (Lithium iron phosphate) have the highest energy density (141.55 wh/kg) currently available in the market, for any LFP battery. LFP has proven to be far more resilient than NMC chemistry, with the latter being more prone to thermal runways. It is also preferable due to the advantages it offers in cell packaging – an advantage Mahindra appears to have maximised. Because even though cells continue to be imported, primarily from China (Until Mahindra’s agreement with VW to source ‘unified’ cells comes into play in 2026), the packaging and more importantly the extensive testing procedures are what determine their efficacy in a climatically extreme environment like India.
The facility is Velusamy’s brainchild, with a lot of advanced equipment hand-picked by the man himself. This includes Field Emission Scanning Electron Microscopes designed to analyse microstructure and morphology of electrodes, an X-Ray Diffractometer, a CT scanner (for non-destructive analysis of cells) an accelerating rate calorimeter (for thermal safety and abuse tests) and much more. The battery packs are placed within lightweight aluminium brackets with extrusions that are compliant with a 200 kilo newton side pole crash test.
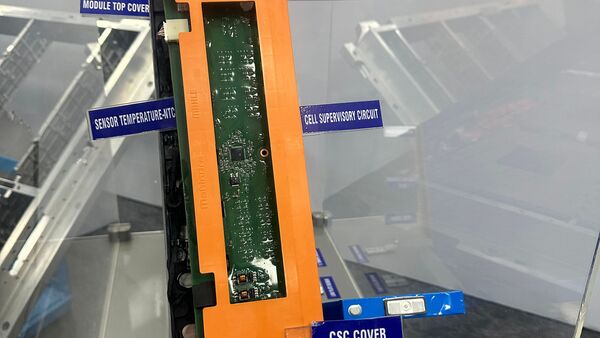
The testing measures for the battery packs are extensive. According to Mahindra, the standard procedure, in accordance with what Indian regulators have put in place, involves a 30 minute battery water immersion test, given that water leakage is a major concern. Mahindra however, subjects their battery packs to 12 hours, 24 hours and even 48 hour tests, claiming that the battery remains intact. According to a brand executive “To qualify for IB 67 certification, you need to immerse the battery in pressure depths up to four bar. We’ve done it up to 10 bar. In fact we have even gone up to 100 bar and then applied 80 degree centigrade temperature. Mahindra has also tested how the anode material in each battery fares after 1 lakh kilometers. The INGLO platform, at present, boasts of 152 patents.
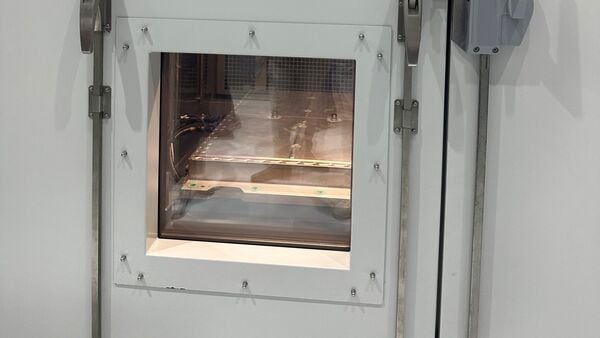
We then come to the extensive series of vibration tests via a high-frequency, low-amplitude vibration tester. At the launch of the EVs, R Velusamy talked about how, given the undulated road conditions in India cause the vehicle to accelerate laterally and upwards, and as such, particularly extensive battery testing measures need to be put in place. At a test bed in the facility, the battery packs are subject to g-forces upwards of 7gs. Lateral force is applied in gradual steps, going from one g to eight g followed by a random application of over 40 hours of endless vibrations. LFP batteries in general, are designed to withstand greater temperature extremities. At the facility, Mahindra subjects each pack to a consistent temperature of 50 degrees centigrade and then immediately, subject it to -30 degrees. The temperature chamber is placed right next to the vibration tester, taking the temperature as high as +80-deg C. Each battery pack has a cooling plate under it, so that regardless of the ambient temperature, the battery offers consistent performance. This is yet to be tested, but rival Indian EVs in the recent past have shown a considerable drop in range, in cold areas – something which Mahindra intends to address.
Watch: Mahindra BE 6e review: Fast & furious, is it India’s best EV yet? | Features, range, performance
These measures have undoubtedly been applied by many EV makers, but while several manufacturers have sought expertise and equipment based in foreign locations, Mahindra has over the years, developed a facility that does everything in-house. This includes a series of rapid discharge cycles under high temperatures. Each rapid discharge cycle takes up to 30 minutes. Mahindra subjects the battery to up to 686 such cycles. “It takes about 10 months of testing. We have tested two battery packs in Germany as we did not have the facility available here. Now we do" said the tech executive demonstrating the testing procedures."
Mahindra has also ensured that the battery packs are as fireproof as possible. A wiring harness runs through the entire battery pack, and in the event of a short circuit it immediately disconnects. Even if the battery detects conditions similar to a crash, it immediately disconnects from the entire system. Having attained kilowattage of 79 kWh from an LFP battery is an achievement unto itself, claims the brand. But ensuring that every possible stringent testing procedure is in place to offer consistent range and performance is key. It remains to be seen just how well Mahindra’s new battery packs fare in the real world, but given the extensive testing measures on display at the brand’s R&D facility, the Indian EV ecosystem just got a big boost.